Field Quality Control for Below-Grade Waterproofing
Author: Sheryll Poe | August 7, 2024
Below-grade waterproofing is an important step to ensure a building is safe and dry. But how can contractors certify the quality of this type of waterproofing application on their next waterproofing project? That's where field quality control testing comes in.
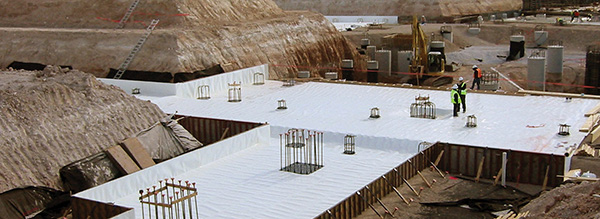
What Is Below-Grade Waterproofing?
Below-grade waterproofing is a waterproofing material that is applied to surfaces below ground level, such as foundations and tunnels, to prevent moisture or water from entering the lowest level of a structure and impacting the levels of moisture and humidity and impacting critical space and equipment.
This type of waterproofing, when combined with other water management techniques, keeps the building free of leaks and protects the structural integrity of the building. This is especially important for buildings with concrete and shotcrete below-grade under slabs or foundations, since these are porous materials that are susceptible to water filtration.
In addition, waterproofing below-grade surfaces can prevent the buildup of moisture, which can lead to the growth of mold and mildew, both of which can compromise indoor air quality and lead to health problems.
How Is Below-Grade Waterproofing Applied?
This type of waterproofing involves the application of liquid-applied coatings or prefabricated sheet membranes to the below-ground surfaces of a building's walls.
Liquid-applied coatings can be applied to vertical or horizontal surfaces pre- or post-construction, making them a good fit for below-grade applications. Liquid-applied coatings can be easily mixed at the jobsite and applied using a squeegee, roller, trowel or spray equipment.
Membranes are commonly used on exterior below-grade surfaces. All new construction has either dampproofing or waterproofing applied before backfilling. Sheet membranes are supplied at a specific thickness and are applied to a primed substrate. This eliminates the need for thickness checks and allows for a wider labor pool for installation.
Below-grade waterproofing is offered in a variety of technologies from multiple brands. Additionally, there are innovative waterproofing membranes containing the latest scientifically enhanced materials, such as waterproofing geotextiles, high-density polyethylene (HDPE), polypropylene, and proprietary adhesives.
What Is Field Quality Control Testing, and Why Is It Important?
Waterproofing failures are not always easy to spot. Field quality control testing ensures that the waterproofing is installed correctly and performs effectively. Because waterproofing is such an important component and applications can vary widely, field quality control testing is critical both during the application process and after.
There are several variables that can affect the installation of below-grade waterproofing, including substrate strength, moisture content, application thickness and surface preparation. To ensure optimum waterproofing material performance, field testing is essential.
There are a number of tests involved in ensuring field quality control on a project, including substrate condition, surface preparation, installation techniques, or ambient conditions before, during and soon after installation. According to the International Institute of Building Enclosure Consultants (IIBEC), a number of industry-accepted protocols and testing guidelines are used to evaluate all these influences from a number of organizations including IIBEC, the International Concrete Repair Institute (ICRI); the Sealant, Waterproofing and Restoration Institute (SWRI); the Society for Protective Coatings (SSPC); and the American Concrete Institute (ACI).
To prepare for a field quality control test, a contractor or inspector should make sure the substrates have been prepared properly before the waterproof system was installed, that all adhesives and primers were applied properly, that primers were applied and ready before the system was put in place, and that overlaps and other seals have been properly sealed against any penetrations.
Don't Skimp on Waterproofing Below Grade or Field Testing
It is only by conducting a field quality control test that a contractor can ensure that they've done everything to achieve the best possible result on a project and that they've also met all the manufacturer's recommendations and warranty requirements.
Field testing a waterproofing system is an important and reassuring final step to a waterproofing project, so be sure to keep detailed records of all inspections and tests made during the entire process.